What is PDCA (Plan-Do-Check-Act)? PDCA, also known as the Deming Cycle or Shewhart Cycle, is a continuous improvement model used in business and other fields to improve processes and products.
It is an iterative four-step process that involves planning, doing, checking, and acting. The PDCA cycle is often used in conjunction with other quality improvement tools, such as Six Sigma and Lean.
The PDCA cycle was developed by Walter Shewhart in the 1930s and was later popularized by W. Edwards Deming. Deming believed that the PDCA cycle was essential for continuous improvement and that it could be applied to any process or product.
The PDCA cycle is a powerful tool that can be used to improve processes and products in any industry. It is a simple and effective way to identify and address problems, and it can help organizations to achieve their goals.
PDCA (Plan-Do-Check-Act)
PDCA is an iterative four-step process that involves planning, doing, checking, and acting. It is a powerful tool that can be used to improve processes and products in any industry.
- Planning: The first step in the PDCA cycle is to plan what you are going to do. This includes identifying the problem that you are trying to solve, and developing a plan to address the problem.
- Doing: The second step is to do what you have planned. This involves implementing your plan and carrying out the necessary tasks.
- Checking: The third step is to check your results. This involves evaluating the effectiveness of your plan and identifying any areas where you can improve.
- Acting: The fourth step is to act on your findings. This involves making changes to your plan based on your evaluation, and implementing those changes.
- Continuous Improvement: The PDCA cycle is an iterative process, which means that it can be repeated over and over again. Each time you go through the cycle, you will learn more about your process and how to improve it.
The PDCA cycle is a powerful tool that can be used to improve any process or product. It is a simple and effective way to identify and address problems, and it can help organizations to achieve their goals.
Planning
Planning is an essential part of the PDCA cycle. It is the step where you identify the problem that you are trying to solve, and develop a plan to address the problem. Without a good plan, it is impossible to achieve your goals.
- Problem Identification: The first step in planning is to identify the problem that you are trying to solve. This may seem like a simple task, but it can be difficult to pinpoint the root cause of a problem. Once you have identified the problem, you can begin to develop a plan to address it.
- Goal Setting: Once you have identified the problem, you need to set goals for what you want to achieve. These goals should be specific, measurable, achievable, relevant, and time-bound. Having clear goals will help you to stay on track and measure your progress.
- Action Planning: Once you have set your goals, you need to develop an action plan. This plan should outline the steps that you need to take to achieve your goals. The action plan should be specific, realistic, and time-bound.
- Resource Allocation: Once you have developed an action plan, you need to allocate resources to implement the plan. This may include financial resources, human resources, or other resources.
Planning is an essential part of the PDCA cycle. It is the step where you identify the problem that you are trying to solve, and develop a plan to address the problem. Without a good plan, it is impossible to achieve your goals.
Doing
The "Doing" step is a critical part of the PDCA cycle. It is the step where you put your plan into action and actually make things happen. Without this step, all of your planning will be for nothing.
There are a few key things to keep in mind when you are implementing your plan:
- Follow the plan: It is important to follow your plan as closely as possible. If you make changes to your plan, be sure to document them so that you can track your progress.
- Be flexible: Things don't always go according to plan, so be prepared to be flexible and make adjustments as needed.
- Track your progress: It is important to track your progress so that you can see what is working and what is not. This will help you to make informed decisions about how to improve your plan.
The "Doing" step is an essential part of the PDCA cycle. It is the step where you put your plan into action and actually make things happen. By following these tips, you can increase your chances of success.
Checking
The "Checking" step is a critical part of the PDCA cycle. It is the step where you evaluate the effectiveness of your plan and identify any areas where you can improve. Without this step, you will not be able to learn from your mistakes and make improvements.
There are a few key things to keep in mind when you are checking your results:
- Compare your results to your goals: The first step is to compare your results to your goals. This will help you to see how well you have achieved your goals.
- Identify areas for improvement: Once you have compared your results to your goals, you need to identify any areas where you can improve. This may involve identifying areas where you did not meet your goals, or areas where you could have done better.
- Make changes to your plan: Once you have identified areas for improvement, you need to make changes to your plan. These changes may involve changing your goals, changing your strategies, or changing the way you implement your plan.
The "Checking" step is an essential part of the PDCA cycle. It is the step where you evaluate the effectiveness of your plan and identify any areas where you can improve. By following these tips, you can increase your chances of success.
Acting
Acting is the fourth and final step in the PDCA cycle. It is the step where you make changes to your plan based on your evaluation, and implement those changes. Without this step, all of your planning and checking will be for nothing.
There are a few key things to keep in mind when you are acting on your findings:
- Make sure that the changes you make are based on your evaluation. Do not make changes for the sake of making changes.
- Make sure that the changes you make are realistic and achievable. Do not set yourself up for failure.
- Implement your changes in a timely manner. Do not wait until it is too late.
Acting is an essential part of the PDCA cycle. It is the step where you put your plan into action and make improvements. By following these tips, you can increase your chances of success.
Here is an example of how the PDCA cycle can be used in a real-life setting:
A company is experiencing a decline in sales. The company uses the PDCA cycle to identify the problem and develop a plan to address the problem.
- Plan: The company identifies the problem as a lack of marketing. The company develops a plan to increase marketing spending.
- Do: The company implements the plan and increases marketing spending.
- Check: The company evaluates the results of the plan and finds that sales have increased.
- Act: The company continues to increase marketing spending and sales continue to increase.
This is just one example of how the PDCA cycle can be used to improve a process or product. The PDCA cycle is a powerful tool that can be used in any industry to improve quality and efficiency.
Continuous Improvement
The PDCA cycle is a powerful tool for continuous improvement. It is a simple and effective way to identify and address problems, and it can help organizations to achieve their goals. The PDCA cycle is based on the idea that there is always room for improvement, and that by constantly evaluating and improving our processes, we can achieve better results.
Continuous improvement is essential for any organization that wants to stay ahead of the competition. In today's rapidly changing business environment, organizations that are not constantly improving their processes will quickly fall behind. The PDCA cycle is a valuable tool for organizations that want to stay competitive and achieve their goals.
Here are some examples of how the PDCA cycle can be used for continuous improvement:
- A manufacturing company can use the PDCA cycle to improve the quality of its products.
- A software company can use the PDCA cycle to improve the development process of its software.
- A service company can use the PDCA cycle to improve the customer service experience.
The PDCA cycle is a versatile tool that can be used to improve any process or product. It is a simple and effective way to identify and address problems, and it can help organizations to achieve their goals.
By using the PDCA cycle, organizations can:
- Improve the quality of their products and services
- Reduce costs
- Increase customer satisfaction
- Stay ahead of the competition
If you are not already using the PDCA cycle, I encourage you to start using it today. It is a powerful tool that can help you to improve your processes and products, and achieve your goals.
FAQs about PDCA (Plan-Do-Check-Act)
PDCA (Plan-Do-Check-Act) is a continuous improvement model used in business and other fields to improve processes and products. It is an iterative four-step process that involves planning, doing, checking, and acting.
Question 1: What are the benefits of using PDCA?
PDCA can help organizations to improve the quality of their products and services, reduce costs, increase customer satisfaction, and stay ahead of the competition.
Question 2: How can I use PDCA to improve my process?
To use PDCA to improve your process, you need to first identify the problem that you are trying to solve. Then, you need to develop a plan to address the problem. Once you have a plan, you need to implement it and track your progress. Finally, you need to evaluate the results of your plan and make adjustments as needed.
Question 3: What are some common mistakes that people make when using PDCA?
Some common mistakes that people make when using PDCA include:
- Not planning adequately
- Not following the plan
- Not checking the results
- Not acting on the findings
Question 4: How can I get started with PDCA?
To get started with PDCA, you can follow these steps:
- Identify a problem that you want to solve.
- Develop a plan to address the problem.
- Implement your plan and track your progress.
- Evaluate the results of your plan.
- Make adjustments to your plan as needed.
Question 5: What are some examples of how PDCA can be used?
PDCA can be used to improve any process or product. Here are a few examples:
- Improving the quality of a product
- Reducing the cost of a product
- Increasing customer satisfaction
- Improving the efficiency of a process
Question 6: What are the key takeaways from using PDCA?
The key takeaways from using PDCA are:
- PDCA is a simple and effective way to improve processes and products.
- PDCA can be used to improve any process or product.
- PDCA is a continuous improvement model, which means that it can be repeated over and over again.
Conclusion
PDCA (Plan-Do-Check-Act) is a powerful tool for continuous improvement. It is a simple and effective way to identify and address problems, and it can help organizations to achieve their goals.
PDCA can be used to improve any process or product. It is a versatile tool that can be applied to any industry or organization.
If you are not already using PDCA, I encourage you to start using it today. It is a valuable tool that can help you to improve your processes and products, and achieve your goals.
Learn All About Synovial Fluid Prices
Get The Latest California Income Tax Rates And Information
A Comprehensive Guide To The Cell Cycle Phases

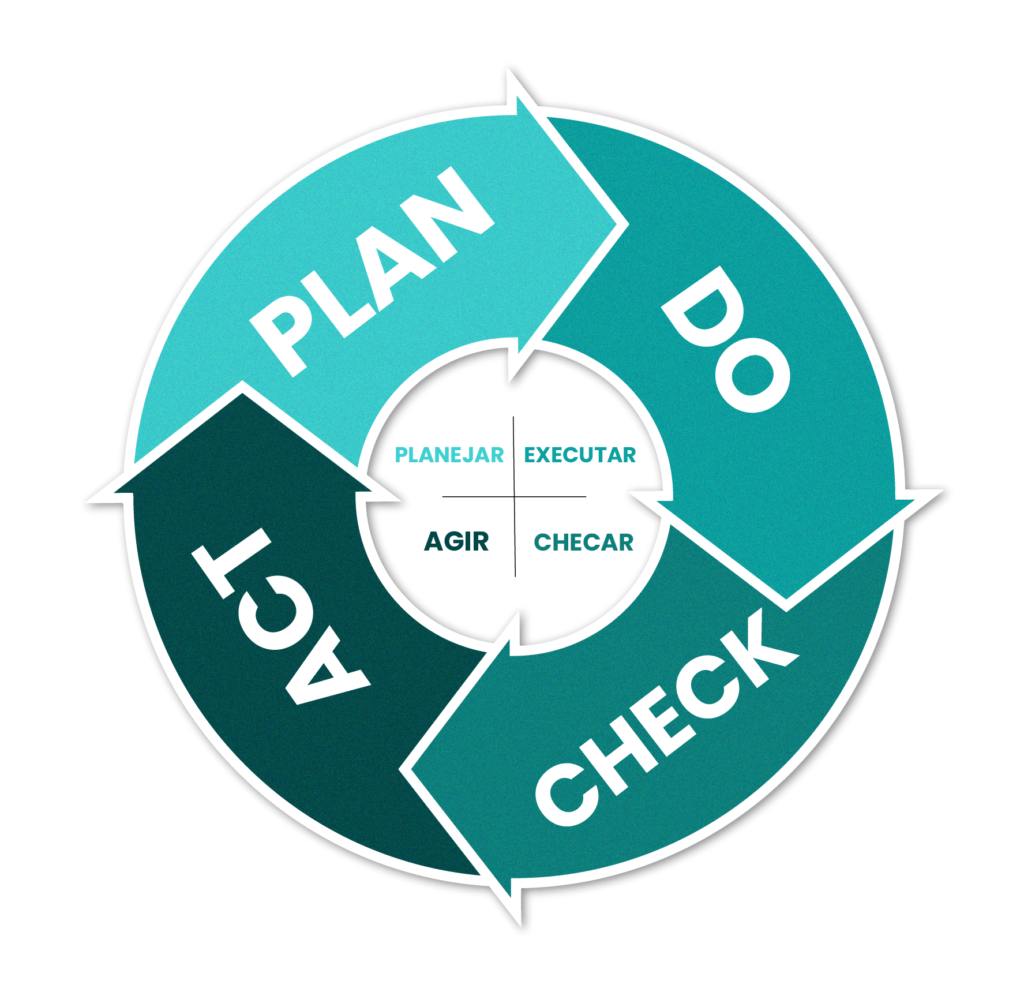